GW Baja SAE Brakes Subsystem
- alexandertgarner
- Jan 24, 2020
- 3 min read
Updated: Aug 27, 2020
Testing and implementing custom aluminum brake rotors as part of a complete subsystem redesign.
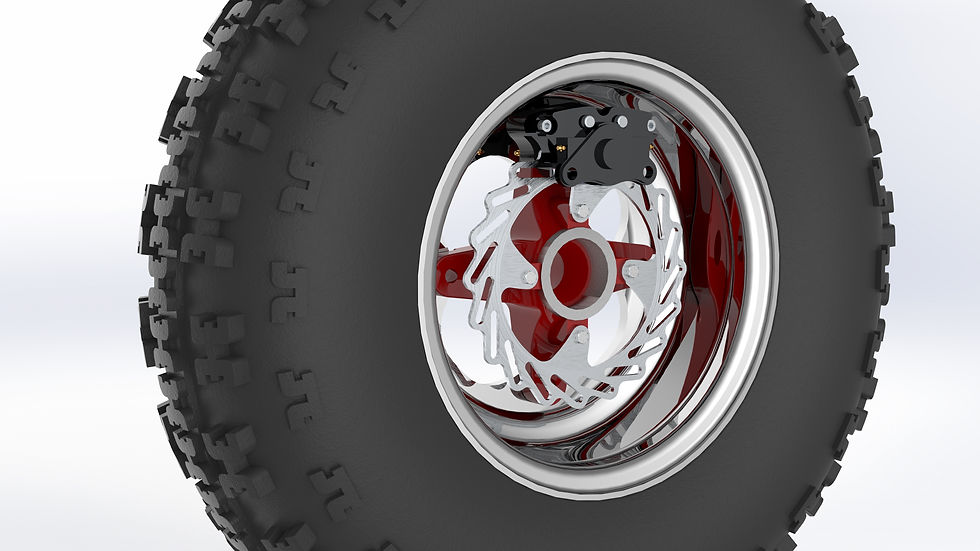
Coming off a successful 2018/2019 season for GW Baja, placing 20th overall at Baja SAE Tennessee Tech, the team was confident we had a strong vehicle to iterate off of. We evaluated the strengths and weaknesses of the 2019 vehicle.
Previous years, 2019 included, the brakes system had largely been left to guesswork; there was minimal confidence in our component selection and whether the vehicle would perform as hoped. At competition, it was difficult to achieve a four-wheel lock, which is necessitated by the rules for safety reasons.
Doing the Math
To begin the redesign, the three-person brakes team researched braking dynamics. Using information from Wong's Theory of Ground Vehicles, my partner, Samir Aziz, automated pages of equations in Excel. Given a set of variables, the sheets would predict braking performance. This Master Spreadsheet became indispensable.
Some of the input variables had to be determined experimentally; for instance, the coefficient of friction between the brake rotors and brake pads. I helped devise and execute these experiments.
The Name of the Game: Weight Savings
For its entire history, GW Baja has used steel brake rotors on the vehicle. Steel was tremendously heavy, and I began researching aluminium, which would offer a substantial weight reduction.
We had some important questions:
Would aluminum hold up under the heat and forces of braking?
How might the wear-rates of aluminum rotors compare to that of steel rotors?
How might we manufacture aluminum brake rotors in house?
Armed with information (required braking torque, etc.) from the Master Spreadsheet, I set out to answer the first question. I taught myself ANSYS and performed a variety of structural simulations, both static and transient, of aluminum rotors under braking forces.
Above: experimenting with transient analysis to produce a more accurate model
I determined, with confidence, that aluminum rotors would easily handle braking forces.
Topology Optimization
Simulations were performed on a 'blank' rotor with no cutouts. Then, I imported FEA results into a Topology Optimization model. As I experimented with different optimization goals, it became clear that Topology Optimization wasn't the tool for us. The 'optimized' rotors had cutouts in undesirable locations. Moreover, lighter rotors could be designed by hand. These lighter rotors safely passed structural simulations.
Below is my first rotor with cutouts: it would be a prototype to test on the 2018/2019 vehicle.

Manufacturing
The GW Machine Shop does not have a Plasma Cutter or Waterjet, so we manufactured the rotors on a four-axis Haas Mini Mill. See a process picture below.
The rotor was machined out of 8x8, 3/16", MIC - 6, 6065 Aluminum. MIC - 6 was chosen because of its superior flatness, which is desirable from a brake rotor. I was confident we could use 0.125" thick aluminum but it would be too thin for the 2018/2019 rear brake caliper.

Below are the finished prototype rotors.

Testing
The aluminum rotors worked wonderfully on the 2018/2019 vehicle. We achieved four-wheel lock easily, as shown in the testing video below.
There was significant wear on the aluminum as a result of using sintered brake pads meant for steel. We were already aware of Wilwood's Purple brake pad compound, designed for use on Aluminum. For the 2020 vehicle, the team had sourced calipers with compatible Purple pads. We were confident that wear rates would be minimal over the course of a 4 hour Endurance Race.
Next Steps: Final 2020 Rotor and More Weight Reduction
After success with the prototype rotor, I was confident the rotor weight could be further reduced. Below is a screenshot from ANSYS of the final 2020 rotor design. Also shown is a render from Solidworks Visualize.

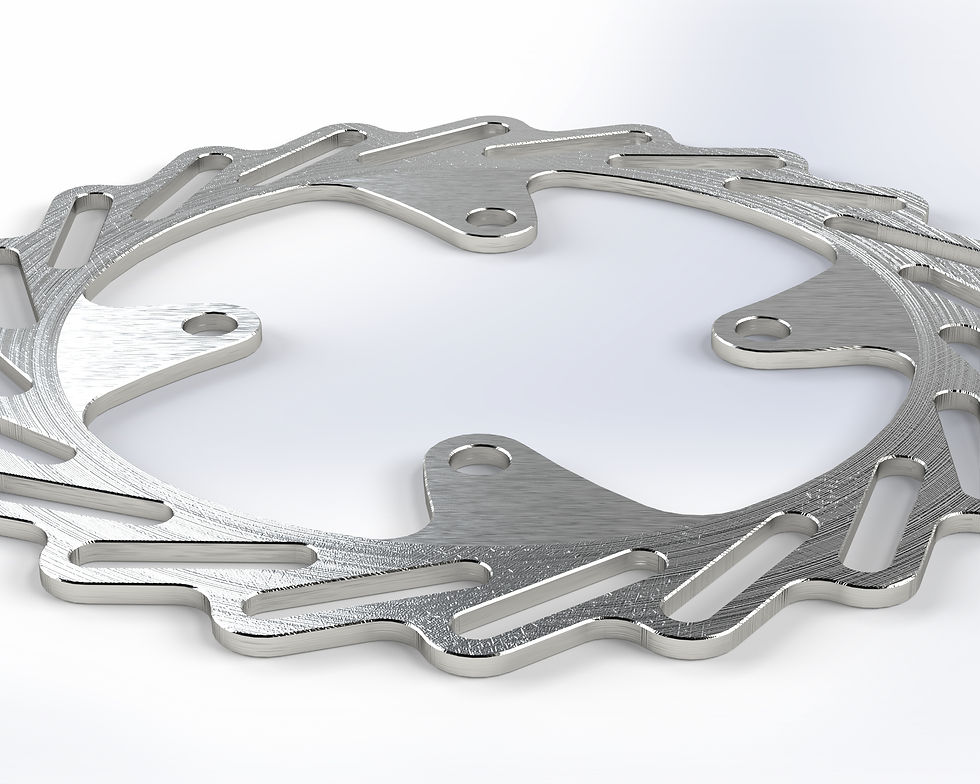
Because of COVID-19 campus shutdowns, we were unable to manufacture the final 2020 rotor. This post will be updated after their completion, hopefully in Fall 2020.
Very nice rotors!